Avoiding Failure in Design
A guide to utilising FMA to catch problems before they happen
When it comes to designing and launching space vehicles, aeroplanes, and cars, product failure of any kind is simply not an option.
Over the past 50 years, the automotive, aerospace, and manufacturing industries have developed front-end design processes that reduce failures and R&D costs whilst improving product quality.
Locus has developed expertise that leverages these Failure Mode Avoidance (FMA) techniques and applies them to product design, though the tools and techniques are not limited to the product design space.
This type of systematic thinking is applicable in any innovation space: process design, software design, attribute improvement, etc.
Failure Mode Avoidance in the NPD Landscape
Increase quality, save time, and reduce R&D costs; it’s a win-win-win situation.
Throughout the product development process, there are on average five engineering changes per part1. The average cost of an engineering change is estimated at $50k2 (resource cost, manufacturing costs, tooling changes, etc).
This generally happens because most designers dive straight into the physical design domain. Issues and failures only become apparent during a test and validation phase just prior to product launch. Then more changes occur just after launch to perfect and finalise the product.
At its worst, you get into the realm of product recalls.
Our FMA tools avoid this by doing the thinking upfront; before money is spent on physical design and on prototyping. We scrutinise any design with a fine-tooth comb, drilling down into its functionality and assessing noise factors which could derail its functioning.
We then embed mitigation and controls into the initial design, reducing the number of prototype phases. By the time the product launches you can be sure that it is transparent to a whole host of noise factors.
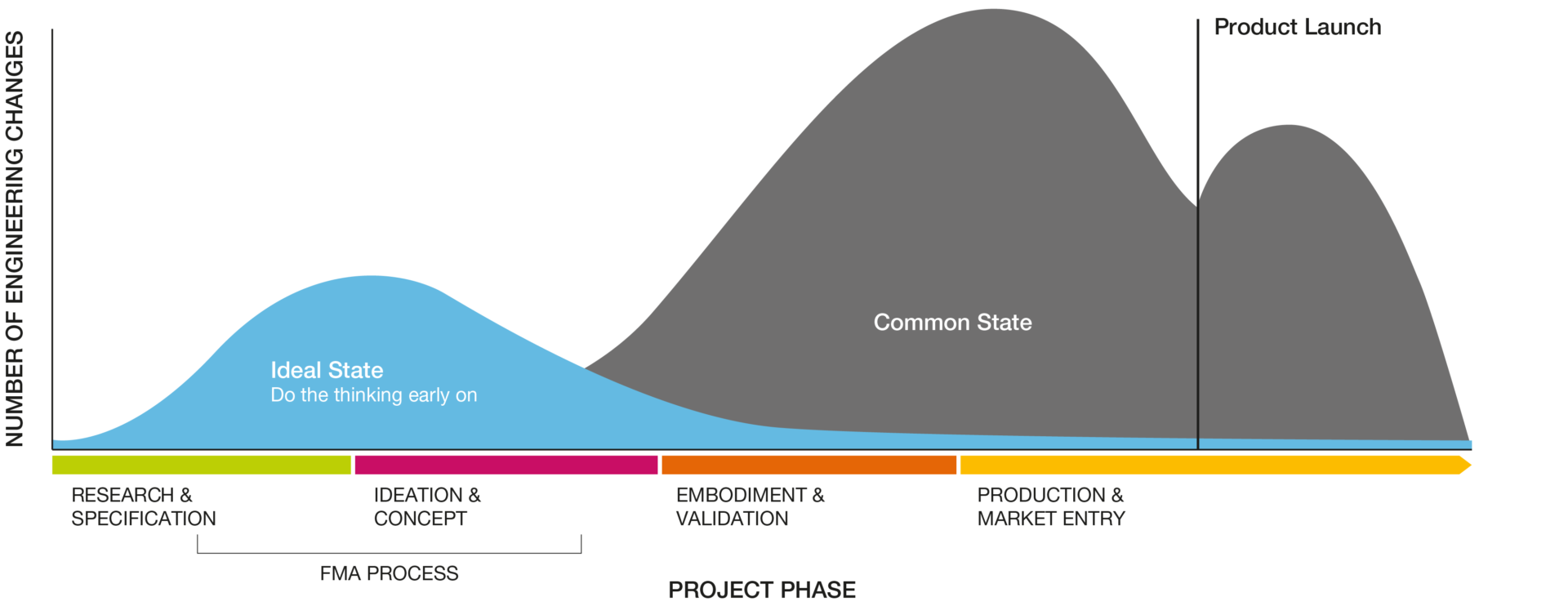
Sources:
1 Cash, P.A.: Right first time production releases. MSc thesis, University of Bradford (2003)
2 Wasmer A., et al.: An industry approach to shared, cross-organizational engineering change handling – The road towards standards for product data processing. Computer-Aided Design (2010)
Landscape Diagram: Rutter, B.G, et al.: Systems Engineering Excellence Through Design: An Integrated Approach Based on Failure Mode Avoidance
A suite of tools and techniques have been developed to help you apply the FMA process to your product or process.
Our FMA approach is underpinned by a functional requirements cascade. We ask, “What does your product/process need to do, and how does that cascade into the functionality of the sub-systems and components that make up the product?”
This means we apply and validate our tools at a total system level, at the sub-system level, and also at the nuts and bolts (component) level. It works the same whether you are in the process design space, manufacturing, or production planning space.

The toolkit
Before we dive into the design work, we need to utilise the tools to answer the most key design question:
“How can I make sure my product performs well under all conditions?”
In the full FMA process, the information from one tool will flow into the next, as shown in the Process Flow diagram below. Each tool will then feed the information used in the D-FMEA. The beauty of FMA is that the tools are modular; this means we can pick and choose which ones best apply to your specific need.
We understand that not everyone has the time or budget and that resources are finite. In most cases, a parameter diagram and FMEA can get you to where you need to be.
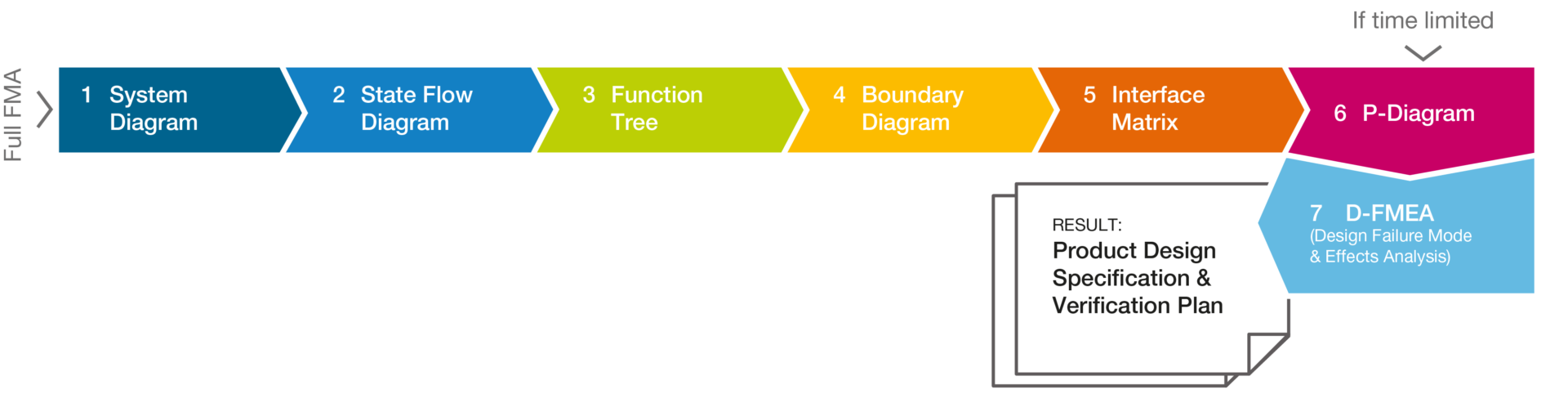